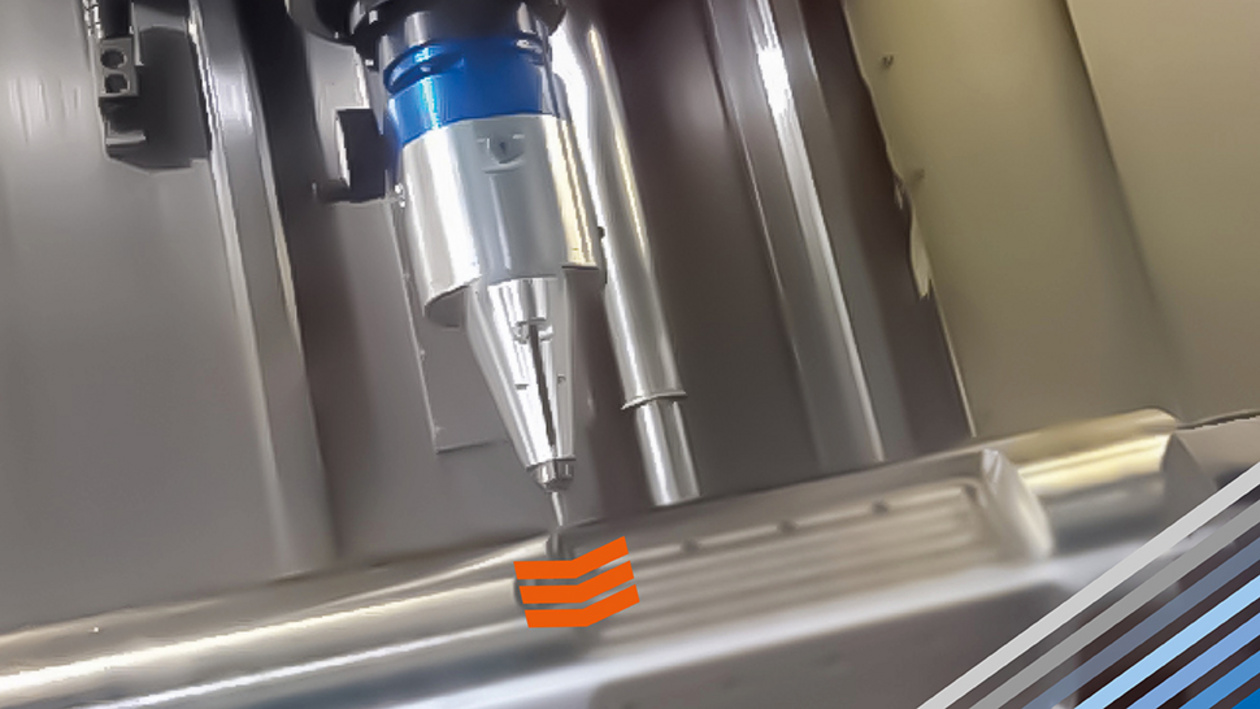
與噴丸或深滾相比,機械錘擊強化零件是一種相對較新的工藝,目前僅用於特殊情況。然而,該工藝具有巨大的優勢,因為它可以更深地影響零件的亞表面積,並且無需任何複雜的機械技術。亞表面積可影響至2-5毫米的深度,而不會對機器施加任何特殊應力。下文我們將探討其原理以及機械錘擊強化的工作原理。
機械錘擊噴丸工藝
顧名思義,機械錘擊強化 (MHP) 是一種使用機器引導工具進行的脈衝機械表面處理。此工藝介於噴丸強化和深滾壓之間。在噴丸強化中,噴丸顆粒以脈衝方式撞擊表面。然而,該製程實際上不可能整合到CNC工具機中。而深滾壓可以整合到任何CNC工具機中。然而,滾動體始終與表面保持持續接觸。成形速度較低,且沒有脈衝成形。
在MHP中,最初幾何形狀完全自由的刀具透過衝擊系統加速,並以高頻衝擊表面。根據刀具類型和製造商的不同,刀具加速方式也有所不同。可使用氣動、電磁或壓電系統。在這些情況下,需要額外的能量來源。使用氣動-機械刀具概念時,無需額外能量源,因為與錘鑽一樣,斜盤通過旋轉運動,進而驅動衝擊系統。活塞和汽缸的運動會產生氣壓,使活塞加速。然後,活塞撞擊刀具刀片,刀片被加速並向表面移動。
所有工具系統的製程本身相同,主要由衝擊頻率、衝擊能量和衝擊距離/覆蓋等參數描述。目前正在製定針對此製程的VDI標準(VDI 3416 Sheet 1),該標準描述並定義了該製程的所有製程參數。除了這些主要參數外,工具刀片的形狀也起著決定性作用。它會影響接觸面,從而影響壓力,並最終影響給定衝擊能量下的表面變形。具有特定半徑的球形刀頭很常見。然而,其他形狀(無論是否具有表面結構)也是可行的。
機械錘擊後的表面形貌
該工藝的運動通常蜿蜒穿過表面。這意味著表面被銼平。進給速度和衝擊頻率的選擇應確保每次衝擊在進給方向上重疊。重疊率通常為 30% 到 80%。重疊率越小,製程效率越高。然後,下一個路徑將按照定義的路徑偏移進行。此處,路徑偏移的選擇也應確保衝擊重疊。
影像顯示了硬度為 47 HRC 的 42CrMo4 材料加工後的表面形貌。衝擊能量 Ekin = 120 mJ,並使用了三種不同的刀尖直徑。可以清楚地看到,表面仍然保持了相當規則的結構。滾壓表面的結構會更均勻。然而,圖像也表明,衝擊能量、半徑和材料必須協調一致。當直徑 d = 50 mm 時,表面幾乎不受相同衝擊能量的影響。
殘餘應力在較大部件深度的形成
然而,這並不適用於殘餘應力的形成。雖然使用這些參數時在表面上沒有明顯的影響,但仍會形成壓縮殘餘應力。因此,錘擊也會對深度產生影響。在這種情況下,如果表面上也能看到塑性變形,則殘餘應力會更大。下圖顯示了直徑為 d = 12 毫米的衝擊頭的殘餘應力深度曲線。可以清楚地看到,壓縮殘餘應力的深度如何隨著衝擊能量的增加而增加。雖然看起來水平相當,因為在 30 和 185 mJ 之間的差異中曲線非常相似,但這裡必須考慮深度。在 E k = 185 mJ 時,深度效應約為 1.75 毫米,而在 30 mJ 時僅為 1 毫米左右。