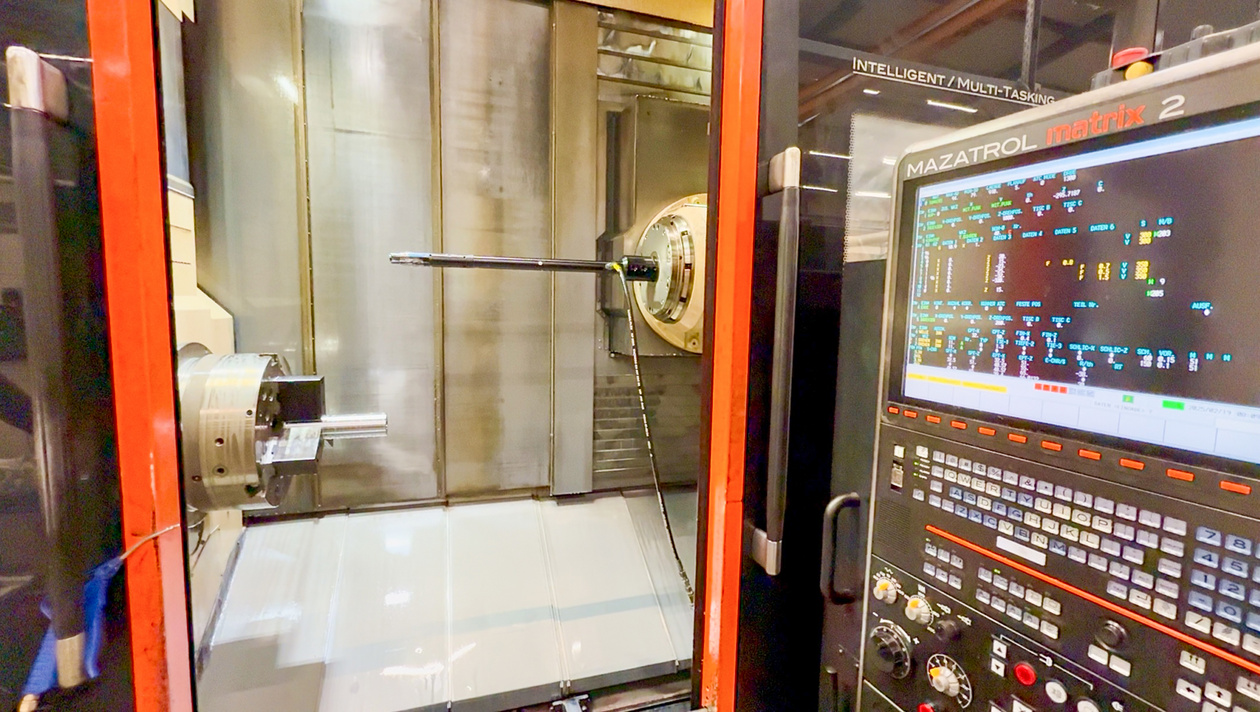
如何在生產中實現 IT8 和 R a <0.1 µm
液壓缸是一種特殊部件,對真圓度和表面粗糙度的要求很高,這使得生產極具挑戰性。同時,液壓缸在機械工程中被視為標準零件。它們使用頻繁,且技術要求不高,這意味著液壓缸的價格相對較低。然而,這也意味著相對複雜的生產也面臨較高的成本壓力。因此,許多製造商專注於優化整個液壓缸的設計和加工,並依賴高品質的半成品。
對於氣缸而言,這意味著使用預加工管材,尤其是在缸管生產中。管材內部已完全加工,只需按長度切割並提供連接尺寸即可。如今,管材生產採用深鑽機床上的刮削和滾壓相結合的工藝。與過去使用的珩磨工藝相比,這顯著縮短了加工時間。
然而,問題在於,在價格上漲的背景下,公司能否在自己的生產設施中使用標準工具機進行完整的加工? 這將提高靈活性,同時大幅降低原材料成本。
SKIOC 用於在標準機床上剝管的工具
因此,ECOROLL 採用了刮削和滾壓工具的原理,並將其改進用於車床或銑床。現在,借助所謂的 SKIOC 工具,管材也可以直接在機床上透過內部刮削進行生產。
這些刀具由一個包含兩把或三把刮削刀的刀體組成。每把刮削刀上前後排列著兩個用於內孔刮削的專用可轉位刀片。首先,預銑刀在孔內形成均勻的尺寸,可以說是清潔了孔。然後,精銑刀加工出最終表面,切削深度p = 0.1 - 0.2 mm。
採用久經考驗的OMEGA原理,打造完美圓形孔形。刮削刀相互影響。它們安裝在浮動軸承上,推入一把刀時,另一把刀也會隨之伸出。導軌引導刀具在現有孔內進行相應的導引。
由於採用兩到三把刮削刀,且刀刃更偏向軸向,因此可實現極高的切割效率。此製程的常見切削速度為 vc = 100 - 300 m/min,進給速度為 f = 1 - 3 mm。
刀具透過冷卻潤滑劑的壓力作動,這意味著刀具不僅能在加工直徑上保持穩定,而且在加工後也能變形,並在快速移動時從孔中拔出。加工過程中不會損壞已加工的表面。機床必須進行相應的改裝才能啟動。此處要求壓力至少為 70 bar,流量為 12-24 l/min。
高流量主要是為了支援排屑。刀具上的噴嘴將切屑從管道中向前噴射出去。遺憾的是,它無法像傳統鑽孔那樣將切屑排出到管道後方。這就引出了機器的第二項技術要求:必須將切屑安全地引導出管道。
夾持裝置的設計必須確保管後方留有開放的切屑空間。例如,如圖所示,夾持裝置後方有一個開放式燈籠狀結構,用於收集和排出切屑。夾緊裝置必須根據工件進行個性化設計。
透過刮削和滾壓實現氣缸管的生產性加工
刮削(即加工製程)已達到IT8的高圓度精度。同時,表面效果也相當令人印象深刻。以客戶測試為例,加工一根42CrMo4材質的管材,我們實現了平均粗糙度深度Rz = 8 µm,算術粗糙度Ra = 2 µm。切削速度vc = 175 m/min,進給速度f = 3.5 mm。
當然,這種表面品質還不足以滿足液壓缸的生產要求。然而,採用傳統的滾壓拋光工藝,以多滾壓機械工具作為最終加工步驟,能夠將表面質量降低至Ra值<0.1 µm。這對於液壓缸的生產已經足夠了。